Reduced water consumption through grinding water treatment
The purchase of a new sanding system was intended to ensure outstanding sanding quality. On the other hand, the question arose as to how the processes could be further optimised in a sustainable and cost-reducing manner. The glass grinding water was to be purified by a professional water treatment system and fed back into the process by means of recirculation. This is because the disposal of waste water into the public sewer is not permitted.
As TARDIS has been generating its own electricity for over 10 years, it was a matter of course to supply the grinding system and grinding water treatment via the company’s own solar panels.
In addition, the waste heat from the compressor was to be utilised as space heating for the production area, thereby reducing CO₂ emissions in the long term.
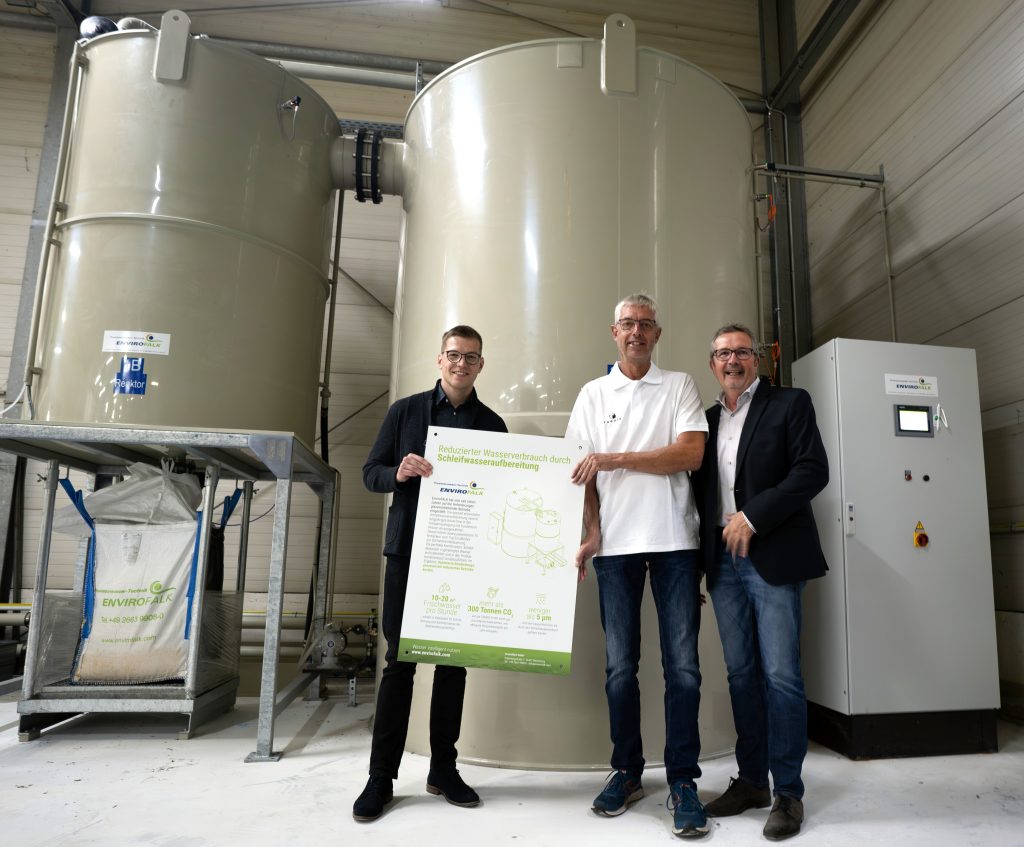
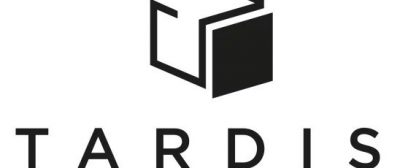
TARDIS GmbH in Neuwied am Rhein has been producing a wide range of products made of toughened safety glass (ESG) since 2005.These include shower enclosures, glass rear walls, room partitioning systems and façades that are customised to suit any room situation.TARDIS not only emphasises individuality and variety, but also sustainability.Through targeted measures such as solar modules on the roof, short transport routes, consistent recycling management and well thought-out water cycles, the company saves more than 300 tonnes of CO₂ every year.
Recognising sustainable water treatment
Glass processing involves cutting, drilling, polishing and grinding. The grinding machine is supplied with large quantities of cooling water. At peak times, it is often 10-20 cubic metres of fresh water per hour. In order to minimise fresh water consumption and consequently reduce costs, the experts at EnviroFALK recommended a pure water circulation system to supply the washing machine in order to wash the processed panes without stains, as well as a recirculating grinding water treatment system.
‘Newly developed glass types and demanding rinsing processes require a high level of process engineering expertise in water treatment,’ says Christoph Gilles, Application Consultant for the glass and solar industry at EnviroFALK. ‘The question that drives us in every project is how the water requirement can be utilised both sustainably and cost-effectively for the area of application in conjunction with the high quality standards.’
In order to optimise the water quality and simultaneously reduce operating costs at TARDIS, the experts at EnviroFALK analysed in detail the performance and functionality of an effective reduction in the particle load in the grinding water circuit. Due to the fine glass particles – smaller than 5 μm – optimum cleaning requires the addition of dosing agents. As a result, the glass particles combine to form larger units and settle more quickly. The resulting sludge is then quickly and effectively dewatered by settling and using the patented EnviModex filter bags and disposed of with very little residual moisture.
Complexity requires solutions
The EnviroFALK grinding water treatment system is characterised by a special system architecture that accelerates the flow in the settling tank. This reduces the time window for the settling process and minimises the need for dosing agents considerably.
Christoph Gilles, Product Manager Glass Industry at EnviroFALK: ‘By adding small quantities of specially selected dosing agents, we can react specifically to the chemical properties of the wastewater. It is important to adjust the dosing quantities precisely to the respective conditions on site.’
From the grinding machine, the dirty water is pumped into the sedimentation tank with the addition of the dosing agents. The rapid reaction of the dosing agents in the dirty water ensures immediate flake formation in the reaction tank. As a result, the glass particles sediment very quickly. The filter bags specially developed and patented by EnviroFALK, EnviModex, dewater the sludge quickly and effectively and can be disposed of easily. If the water quality requirements are high, the clear water can be purified via additional filter stages before being returned to the production cycle.
A 6-week trial run was initially agreed so that Tardis could thoroughly test the grinding water treatment system. ‘We naturally wanted to make sure that the system would also deliver perfect results in 7-day operation,’ says Thomas Breuer-Löwenstein, Managing Partner, adding: ’This concession once again confirmed that we have the right partner on board with EnviroFALK.’ Once the grinding water treatment system had successfully passed the test, it went seamlessly into regular operation.
The convincing track record
The EnviroFALK grinding water treatment system impresses with its high cleaning performance and optimum water quality. The treated water is continuously fed back into the machining process. This has significantly reduced the operating costs in the water balance at TARDIS. The combination of dosing agents, which is precisely coordinated on site, also leads to a further reduction in chemicals. Cost-intensive overdosing of dosing agents is therefore a thing of the past.
Conclusion
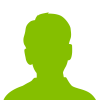
Thomas Breuer-Löwenstein
Managing Partner at TARDIS